Crece el reto de transportar los gigantes eólicos por carretera
El traslado e instalación de los aerogeneradores, progresivamente más voluminosos, supone un desafío logístico y de costes cada vez mayor
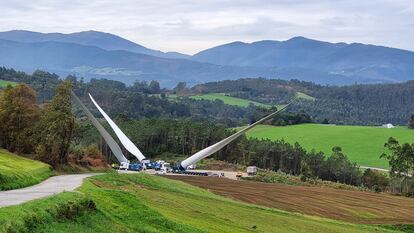
Salvados los obstáculos administrativos, llevar un aerogenerador de la fábrica al terreno elegido para su puesta en marcha es una operación logística bastante delicada que en los últimos años se ha complicado aún más por la demanda de máquinas más altas y potentes para generar más electricidad. En la última década, el diámetro medio de los rotores ha pasado de los 90 metros a los 172 metros, casi el doble, indican en la firma Vestas. En cuanto a la potencia, desde Siemens Gamesa apuntan que lo normal hoy en día son turbinas terrestres de más de 4 MW e incluso de más de 5 y 6 MW en algunos proyectos. En offshore, donde la altura no es un problema, se están instalando aparatos de 13-15 MW y se espera que en los próximos años se alcancen los 20 MW, informan en AEE.
Así que mover estos mastodontes por carreteras de montaña sinuosas y con pendientes muy pronunciadas “requiere una atención especial y, en ocasiones, puede llegar a convertirse en un proyecto complementario”, confirman fuentes de Iberdrola. La adversidad es mayor cuando la ruta exige atravesar cruces con líneas de media tensión, núcleos de población con calles estrechas, zonas boscosas o puentes antiguos que requieren de alguna intervención o, incluso, la construcción de un desvío para evitarlos.
La aparición en 2019 de Blade Lifter, un elevador hidráulico que permite transportar las palas en posición inclinada sobre un tráiler de 10 ejes, ha aliviado el problema. El sistema puede levantar las torres hasta unos 65 grados e incluso girarlas para evitar el efecto vela del viento. Iberdrola ha utilizado este método para llevar palas de 70 metros de alto a parques en una zona montañosa de Grecia.
Eneko Sanz, director general de Nabrawind, señala que este avance ha retrasado el desarrollo de componentes modulares, que se puedan transportar por partes y armar en el destino, aunque la tendencia va en esa dirección. Ya en 2017, General Electric lanzó una turbina de 5,3 MW con aspas articuladas, mientras que Vestas presentó en abril de este año un modelo de 7 MW con una góndola que se puede llevar al terreno dividida en tres módulos.
El peso de la logística en los costes de un proyecto eólico varía dependiendo de dónde se instale la infraestructura, si en tierra o mar adentro. Un informe del Laboratorio Nacional de Energía Renovable —un centro de investigación patrocinado por el Departamento de Energía de Estados Unidos— “hace una buena aproximación” al desglose de gastos de cada tipología, comenta Eneko Sanz, de Nabrawind.
Distribución del presupuesto
El reporte muestra que en eólica terrestre la fabricación de todos los componentes representa el 70% del coste total, mientras que el de la instalación ronda el 30%. En offshore, el estudio diferencia entre fija y flotante. Así, cuando la turbina está cimentada en el fondo marino, la manufactura supone únicamente el 35%. El resto son gastos asociados a la financiación y, principalmente, al transporte y la instalación.
En las plataformas flotantes, “por tratarse de una tecnología menos madura, los costes de instalación todavía son mayores”, explica Sanz. De ahí que solo el 25% del presupuesto se vaya en la fabricación de los equipos y la base se lleve el 37% del capital. “No obstante, es de esperar que conforme se vayan optimizando estas nuevas tecnologías y reduciendo el precio mínimo al que se necesita vender la energía para garantizar la rentabilidad del parque, el propio aerogenerador recobre importancia”, sostiene.
Fábricas cercanas
Ignacio Mora, de Vestas, señala que el despliegue masivo y global de la eólica marina requerirá tener más fábricas cerca de las zonas más activas, para evitar largos desplazamientos en barcos de gran calado que prevén también serán un elemento escaso, por lo que “se necesita cerrar acuerdos con sus fabricantes lo antes posible”.
Sven Seifert, director de logística de Siemens Gamesa, coincide en que la eólica marina requiere de elevadas inversiones en buques, además de infraestructuras portuarias, almacenes y espacios de premontaje. Por eso, el grupo tiene fábricas de aspas y góndolas offshore en puertos como el de Le Havre, en Francia.
Arduos permisos para circular
Ni el tamaño de los componentes, ni las limitaciones de gálibo, las excesivas pendientes o los reducidos radios de giro de las carreteras. La mayor dificultad que se están encontrando los promotores de parques eólicos para llevar los aerogeneradores hasta los emplazamientos es la burocracia. Por su dimensión y peso, el transporte de las palas, góndolas y torres requiere de un permiso de circulación emitido por la Dirección General de Tráfico (DGT), previo informe vinculante del titular de la vía, que normalmente es la Dirección General de Carreteras (DGC). Un trámite “rutinario y sencillo” que, según la Asociación Empresarial Eólica (AEE), está tardando entre tres y cuatro meses, “lo que puede conllevar retrasos en la construcción y el riesgo de que se agoten los plazos de conexión a la red”.
Carlos Arenal, ingeniero de proyecto del departamento técnico de la AEE, explica que la DGC impone a los transportistas requerimientos “desproporcionados y que exceden sus competencias, hasta tal extremo que resultan imposibles de cumplir”. Desde el Ministerio de Transportes aseguran que la DGC resuelve todos los expedientes dentro del plazo legal, que es de tres meses, y que no hay un informe pendiente que haya agotado este plazo.
Tu suscripción se está usando en otro dispositivo
¿Quieres añadir otro usuario a tu suscripción?
Si continúas leyendo en este dispositivo, no se podrá leer en el otro.
FlechaTu suscripción se está usando en otro dispositivo y solo puedes acceder a EL PAÍS desde un dispositivo a la vez.
Si quieres compartir tu cuenta, cambia tu suscripción a la modalidad Premium, así podrás añadir otro usuario. Cada uno accederá con su propia cuenta de email, lo que os permitirá personalizar vuestra experiencia en EL PAÍS.
¿Tienes una suscripción de empresa? Accede aquí para contratar más cuentas.
En el caso de no saber quién está usando tu cuenta, te recomendamos cambiar tu contraseña aquí.
Si decides continuar compartiendo tu cuenta, este mensaje se mostrará en tu dispositivo y en el de la otra persona que está usando tu cuenta de forma indefinida, afectando a tu experiencia de lectura. Puedes consultar aquí los términos y condiciones de la suscripción digital.